The back sheet in solar panel—also known as backsheet or solar backsheet film—is a critical multi-layer component on the rear side of photovoltaic modules. It safeguards solar cells from environmental factors such as UV, moisture, and electrical stress, directly impacting long-term performance and lifespan.
Global Market Insight: According to MarketsandMarkets, the global solar backsheets market size was valued at USD 2.1 billion in 2022 and is projected to reach USD 3.4 billion by 2027, at a CAGR of 10.1%.
Key drivers for the solar backsheets market:
- Rise in photovoltaic installations worldwide (300+ GW cumulative by 2023, per IEA)
- Demand for enhanced durability (25+ years module life expectation)
- Adoption of eco-friendly & high-performance materials (e.g., PET, PVDF, Tedlar®)
- More modules designed for complex/harsh environments: floating PV, desert, BIPV, etc.
Parameter | PET Backsheet | PVF/Tedlar Backsheet | PVDF Backsheet | Fluorine-free Backsheet |
---|---|---|---|---|
Tensile Strength (MPa) | 120–170 | 150–190 | 160–200 | 110–150 |
UV Resistance (years) | 20–25 | 25–30 | 25–30 | 15–20 |
Water Vapor Transmission Rate (g/m2·day) | ≤1.0 | ≤0.8 | ≤0.9 | ≤1.2 |
Thickness (μm) | 250–350 | 250–380 | 250–380 | 200–300 |
Cost (Index, PET=1.0) | 1.0 | 1.6–2.0 | 1.5–1.7 | 0.9–1.1 |
Common Applications | Standard modules | Premium, high-durability | Humid/harsh areas | Urban/BIPV, cost-sensitive |
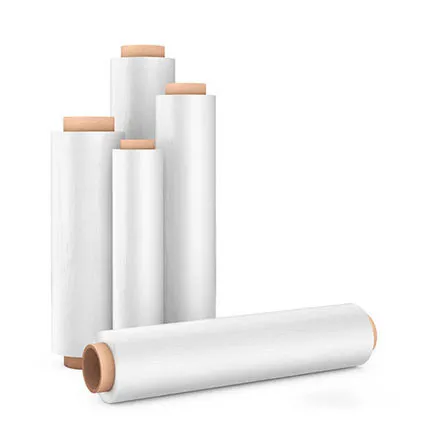
PET/PVDF/PVF, EVA, adhesives → 2. Extrusion/Calendering
Melting & sheet formation (CNC controlled) → 3. Layer Lamination
Multi-layer stacking under heat & pressure → 4. Surface Treatment
Chemical/Corona/Foil embossing → 5. Precision Cutting (CNC)
Thickness & width via CNC/sheeting line → 6. Inspection & Testing
ISO/ANSI UV, adhesion, electrical tests
The process includes advanced extrusion—ensuring material purity—along with CNC-guided thickness control, lamination under precise temperature/pressure (crucial to interlayer adhesion), and multi-standard inspections (ASTM, IEC 61215/61730, ISO 9001 certificates standard for tier-1 suppliers). Surface treatment (e.g., corona, plasma activation) improves adhesion to encapsulants like EVA and enhances weather durability.
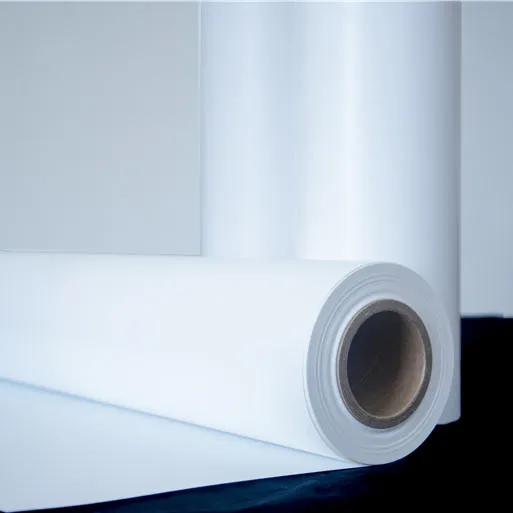
- Material Choices: PVDF (Polyvinylidene Fluoride), PET (Polyethylene Terephthalate), PVF (Polyvinyl Fluoride), EVA-based composites
- Precision: Typical thickness control: ±5 μm, width tolerance: ±0.3%
- Standards: Meet or exceed IEC 61215, IEC 61730, UL 1703, ISO 9001/14001
- Life Expectancy: ≥25–30 years field service (proven by accelerated aging & UV/weathering test data)
For demanding, high-efficiency solar projects, the Lucky Tpcw2 Solar Backsheet sets a new benchmark for reliability and performance in the back sheet in solar panel category. Engineered and refined by LK International, this laminate product features:
Parameter | Lucky Tpcw2 | Conventional PET Backsheet | Premium PVDF Backsheet |
---|---|---|---|
Structure | Triple-layer: PVDF / PET / EVA | PET / EVA | PVDF / PET / EVA |
Tensile Strength (MD/TD) | 175 / 162 MPa | 135 / 125 MPa | 165 / 156 MPa |
UV Resistance | >30 years (5800h+ UV Test) | ~22 years | >28 years |
Water Vapor Transmission Rate | 0.72 g/m2·day | 1.1 g/m2·day | 0.9 g/m2·day |
Dielectric Strength | ≥17 kV/mm | ~12 kV/mm | ~15 kV/mm |
Color Options | White, Black, Transparent | White only | White/Black |
IEC/ISO/UL Compliance | IEC 61215/61730, ISO 9001, UL 1703 | IEC 61215 | IEC 61215/61730 |
Service Life | ≥30 years | 20–22 years | 25–28 years |
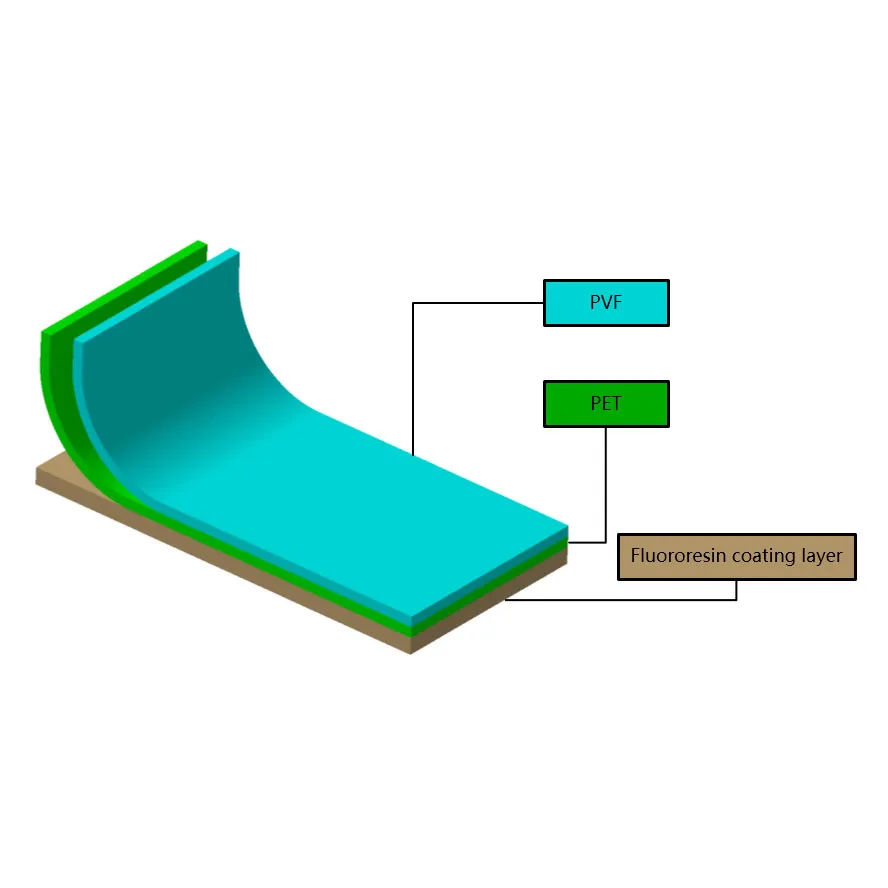
- Advanced Laminate Technology: 3-layer coextrusion for maximum barrier & mechanical strength
- Environment Adaptability: Designed for high-humidity, salt-mist, ammonia, or high-altitude applications
- Customization: Sheet color, thickness, width and embossing tailored for BIPV or utility projects
- Certifications: IEC, ISO, UL recognized, >280 global OEM partners, 18+ years production record
- Warranty: 10–15 years product warranty; insured by international liability insurers
5.1. Application Scenarios
- Utility-scale PV Plants: Large ground arrays in desert (e.g., China Qinghai Solar Park: >1.5 GW PV installation utilizing fluorinated backsheets for maximum sandstorm resistance).
- Rooftop C&I Projects: BIPV and commercial rooftops worldwide (PVDF backsheets preferred for longer life; proven thermal cycling up to 1000 cycles without delamination).
- Floating PV: Lake and coastal installations. Lucky Tpcw2 Solar Backsheet used in German floating PV pilot, reducing moisture-induced PID by 40% vs regular PET backsheets.
- Specialty/Off-grid PV: Mining, telecom, and oil & gas telemetry — where chemical resistance is critical.
5.2. Real-world Performance
- Case: Southeast Asia 50MW Plant (2022)
Lucky Tpcw2 Solar Backsheet: Observed zero backsheet failure after 24 months, against control group with PET showing 1.2% module failures. - Customer Feedback: Project managers note “significantly reduced backsheet cracking and much easier module handling during installation.”
- After-Sale Support: LK International’s on-site inspection and 48h replacement service for critical power projects (see product service terms).
Manufacturer | Main Product Family | Material Tech | Warranty (years) | Certifications | Global Projects |
---|---|---|---|---|---|
LK International (Lucky Tpcw2) |
Lucky Tpcw2, PET/PVDF, EVA-based backsheets | Triple-layer PVDF/PET/EVA | 15 | IEC 61215/61730, ISO 9001, UL 1703 | 280+ OEMs, Asia, EU, North America |
Cybrid Technologies | Cybrid SFC, PET, PVDF, Tedlar | PET, PVDF, PVF | 12 | IEC, TUV, ISO, UL | Global, 10 GW+ |
Dunmore (Steel Partners) | DUN-SOLAR | Tedlar/PET, Fluoro | 10–12 | IEC, UL, ISO | North America, Europe |
Jolywood | NTOPCon, Backsheets | PET, PVDF, composite | 12 | IEC, TUV, ISO | Global, 7 GW+ |
- Custom Specification: Thickness (250–420μm), width (up to 1300mm), surface embossing, color (white/black/clear), with laser or CNC precision
- Lead Time: Standard orders fulfilled in 16–25 days; urgent deliveries in 7–10 days upon request
- Warranty: Standard warranty 10–15 years, upgradable to 25 years for utility/critical industrial projects
- Quality Assurance: Full batch traceability, in-house lab testing, third-party (TÜV, SGS) periodical audits
- Technical Support: On-site module integration instructions, after-sales diagnostics, 24/7 response
Q1: What is the difference between EVA solar backsheet and traditional PET backsheet?
A: EVA solar backsheet incorporates an Ethylene Vinyl Acetate (EVA) layer for enhanced adhesion to cell encapsulants and increased moisture resistance, outperforming PET-only structures especially in humid applications.
Q2: What thickness standards apply to solar backsheets?
A: Most backsheets range from 250μm to 420μm, with IEC 61215/61730 and UL 1703 referencing both thickness uniformity and minimum dielectric strength. Custom thickness is sometimes chosen for ultra-lightweight or high-voltage builds.
Q3: How is the water vapor transmission rate (WVTR) relevant to backsheet selection?
A: WVTR measures moisture permeability; lower values (e.g., <0.8g/m²·day) are better, ensuring solar cells remain isolated and protected, preventing PID (Potential Induced Degradation).
Q4: Which material delivers optimum UV resistance in solar backsheets?
A: Fluoropolymer layers (PVDF, PVF, such as Tedlar™) are industry benchmarks, providing over 30-year UV durability proven by accelerated aging tests and field performance.
Q5: What are the typical testing and quality standards for backsheet of solar panel?
A: Mandatory standards include IEC 61215 (performance), IEC 61730 (safety), and certifications such as ISO 9001/14001 (process), UL 1703 (US safety). Tests cover adhesion, insulation, UV/thermal aging, and flammability.
Q6: Is “solar backsheets” recycling feasible?
A: Yes, modern solar backsheets are increasingly designed for end-of-life recyclability, especially fluorine-free or mono-material PET/EVA backsheets, supporting sustainability goals.
Q7: How does backsheets selection influence module installation?
A: High-tensile, high-barrier backsheets simplify module handling, reduce risk of cracking during mounting, and allow for more flexible framing—crucial for BIPV and large EPC deployments.
- SolarPowerWorld: Backsheet Basics
- PV Tech: Backsheet Failures—Field Experience & Insights
- PV Magazine: Backsheet Reliability—Predicting Module Longevity
For custom technical consultation or backsheet samples, connect with a certified LK International expert or explore the full Lucky Tpcw2 Solar Backsheet product portfolio at www.lkintl.com.